The process begins with the wax injection in molds made beforehand. The mold can be very simple, just like he can be very complicated, according to the desired quantities. A wax model is necessary for every casting. These models are exact copies of the required part.
Casting Process
Step 1
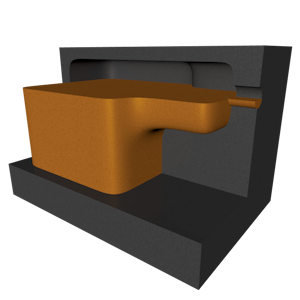
Step 2
Remove the wax models of the mold and assemble them to form a "tree". This one is designed to improve the speed of manufacturing of parts, without sacrificing the quality.
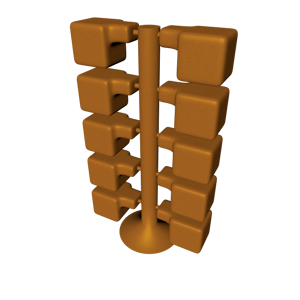
Step 3
The tree is now plunged into a solution of liquid ceramic and then covered with a layer of stucco. This process is repeated from six to seven times to make the shell of ceramic solid enough for the next steps.
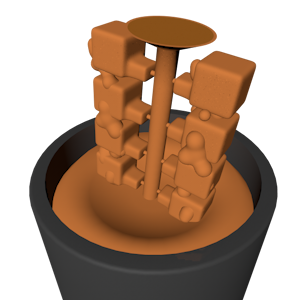
Step 4
The tree covered with ceramic which hardened is placed from now on in an oven to melt the wax and leave the ceramic mold empty with the inside of this one having the shape of the deliberate parts.

Step 5
Once the shell perfectly empty, the necessary metals for parts are then melted and paid into the mold.
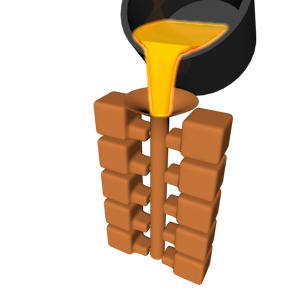
Step 6
Once the metal become solid again, the mold is removed by vibrations and/or by chemical cleaning to leave us the tree with the deliberate parts.
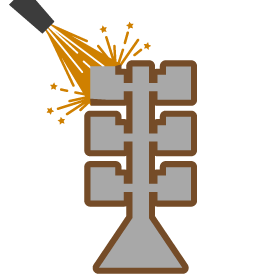
Step 7
The parts are removed from the tree using a wheel of cut or a bandsaw.
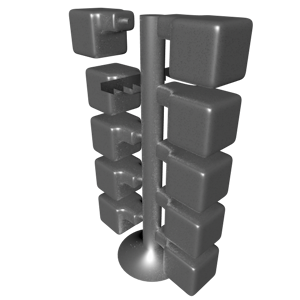
Step 8
It is now the time of the finish. The residues of the tree connected parts as well as any imperfection are removed to finally become the desired part.
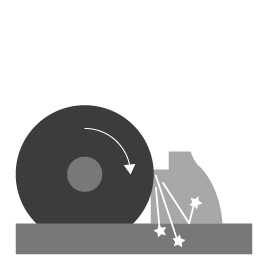
Step 9
Once the product is finished, it is sent at the customer's in desired quantity.
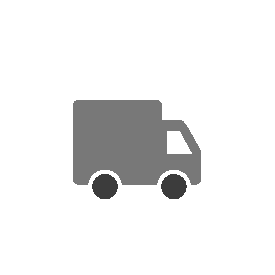
Materials used
Ductile cast iron
Steel
Stainless
Aluminum
(65-45-12)
(8620-8630-30)
(304-316)
(6061-356) Termal threatment T1 to T6